Product Description
Business scope: injection mold, injection molding products, zinc alloy mold, aluminum alloy mold, home appliance mould, gear die mold, bluetooth headset, exquisite small home appliance mould, car DVD, mould, medical mold, pipe box mold, optical mold, terminal mold, auto mold, printer die mold, mobile power supply, and other precision plastic mould.
Mould material: 45 # quenched and tempered, 60 # quenched and tempered, 40 cr conditioning, P20H, 718 h, 2738, 2316, S136, NAK80, NAK80H, S136H, SKD61, SKD11, 718 h for your choice, die set: hard > 30 HRC 45 #
Optimization design of cooling system circulating water, improve the production efficiency, reduce the cost of you
Medium-term processing conditioning, and improve the hardness.
Post-processing nitride (nitride low processing temperature, the deformation is small, no longer need to be hardening is very high (more than HV850) and surface hardness
Abrasion resistance)
Not less than 300000 die die life P20 normal use
Mode of transportation in the mold before shipment must be put locked mode, logistics transport
After-sales service mold 1 year warranty, the warranty period for free repair.
Note: mold in the process of production we will provide customers with mold progress every month
According to the plastic forming theory and experience, design precise mold molding size, ensure products cool setting, without causing more resistance. Guangzhou burleigh fe mould co., LTD. In order to adapt to market demand, improve the utilization rate of production line successfully developed, a double cavity or four cavity of main material and auxiliary material mold. Double cavity of main
Mold has the characteristics of stable production operation is convenient. Factory has always been revered "motto of science and technology is the first productive force", to the technology strives for the development, to quality
Quantity for customer, reasonable cost, with customers sincere cooperation!
SLD Japan Hitachi high wear-resistant alloy cold work tool steels
Ingredient % carbon manganese chrome vanadium molybdenum 1.0 1.0 12.0 0.45 1.5
Delivery status: annealing HB 230 or less
Quenching: preheating first 700 ~ 750 ℃ heating, 1.000 ~ 1.050 ℃, cooling in still air, such as steel with thickness in 6 inches above the heating to 980 ~ 980 ℃, in oil hardening is better
Tempering: heating to 150 ~ 200 ℃ in this temperature, then cooling in still air, tempering should be completed in the second.
Hardness: HRC57 ℃ ~ 62 ℃
Annealing: heating to 800 ~ 850 ℃, and at this temperature for 1 ~ 3 ℃ hours, let it in a furnace, zhejiang cold.
Forging: 1050 ~ 950 ℃
This steel is easy to use: cutting, and appropriate system of sharp blade, scissors, circular saw, cold or hot trimming die, roller, screw, wire mould, milling cutter, punching die solicitation, circular cylinder, the system of power transformer core die, cutting steel sheet rolling knives, steel pipe forming roller, and even chi artisan drum, special forming roller, precision gauges, complex shape of cold pressing tools, tin mold, plastic mold, plastic mold, screw heading die, etc.
DAC Japan Hitachi high-quality hot-work tool steel
0.4 main ingredient % carbon silicon manganese chrome vanadium molybdenum 1.5 1.5 5.3 0.4 1.0
Delivery status: annealing HB250 or less
Forging, 1.050 ~ 850 ℃
Annealing: heating to 800 ~ 850 ℃, the temperature for three hours, let it cool in the oven.
Tempering: heating to 550 ~ 680 ℃ first stay in this temperature, then cooling in still air, tempering should be in the second.
Quenching: heating to 550 ~ 550 ℃, first time heating to 850 ~ 900 ℃
Hardness: HRC53 ℃ below
Purpose: the senior high temperature resistant alloy steel and tungsten steel containing ingredients, suitable for hot-work, aluminum, magnesium, zinc, copper alloy die-casting die, cutting knife, scissors and hot forging, plastic mould, hot reamer, mill knives, general hot forging die and heat between the various tools, etc.
FDAC Hitachi brand special die casting alloy steel
Steel features: FDAC DAC (JIS SKD 61) as the basic ingredients, add to speed up the cutting resistance alloy, the other with special method of manufacturing fast dissolved cut sex has hardened hot-pressing mold.
Features:
1. Their most suitable for use on hardness HRC40-44
2. Was very good, easy processing, mold time shorter
3. Do not need to processing after hardening, free of quenching deformation cracks, expansion, etc.
4. Use the harmful impurity content composition was very low in YSS die casting alloy steel as raw materials in the fine special sponge
5. High resistance to thermal crack, in the high temperature strength, die life is long.
Application: suitable for hot-work, zinc, aluminum, magnesium, aluminum alloy die-casting mould and plastic mould and has the processing does not need to be hardening and deformation characteristic, after appropriate system precision molds or emergency after the advantage of short time internal energy modelling.
Datong steel DC53 Japan "toughness" chrome steel
Features:
1. After heat treatment, hardness higher than SKD11 high temperature 520-530 ℃ after tempering can reach 62-63 HRC hardness is high, more than SKD11 in terms of strength and abrasion resistance
2, toughness is double that of SKD11, DC53 toughness is more prominent in the cold work die steel, therefore, made of DC53 rarely appears cracks and crack, greatly improving the service life.
3, linear cutting machining residual stress is small, after the high temperature temper reduce the residual stress, therefore, a large requirement and the precision of mould in wire-cutting processing after inhibition of crack and deformation.
4, cutting and grinding than SKD11, DC53 cutting and grinding resistance than SDK11. Therefore, use DC53 increases the die life and reduce the processing process.
Purpose:
1, difficult processing materials plastic deformation of the tool
2, other high-speed blanking punch, stainless steel plate punch.
1 / mould process: plan approval - material - machining - die set - mold core processing - electrode processing - mold parts processing - inspection - assembly - fly die - test - production
2 / injection molding process, determine the production line of single - material - confirm that the product quality, structure, size - production - QC inspection - packing.
Mold processing equipment: CNC lathe, walking wire, electric spark, line cutting, high-speed drilling machine, grinding machine, general milling machine, CNC computer gongs.
Plastic processing equipment, precision injection molding machine (80 t - 80 t), 26, tester 5 machines, crusher, mixed color machine 3 units.
Processing capacity: mold design, mold manufacturing and injection molding processing
Mould material: P20H, 718 h, 2738, 2316, S136, NAK80, NAK80H, S136H, SKD61, SKD11, 718 h for your choice, die set: hard > 30 HRC 45 #
Cooling system: optimal design of circulating water, improve the production efficiency, reduce the cost of you.
Processing: mid conditioning, and improve the hardness.
Post-processing: nitride (nitride low processing temperature, deformation is small, no longer need to be hardening and has the very high surface hardness, greater than HV850) and abrasion resistance).
Die life: P20 normal use not less than 100000 times.
Mode of transportation: before the mould shipment must be put locked mode, logistics transport.
After-sales service: mold 1 year warranty, the warranty period for free repair.
Payment Terms︰
Pay 70% deposit first, and confirm OK to pay the balance 30% after products.
Product Image
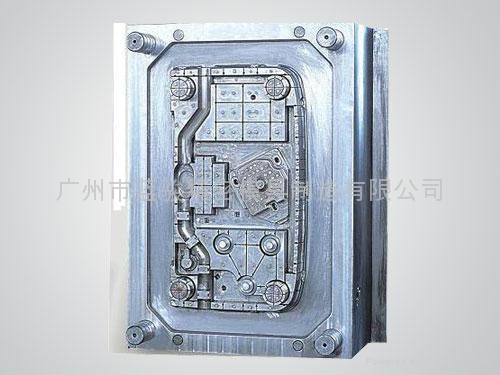

